Plastic extrusion for economical product fabrication
Plastic extrusion for economical product fabrication
Blog Article
Checking Out the Different Methods and Technologies Behind Plastic Extrusion
The realm of plastic extrusion is a blend of development, innovation, and accuracy, essential to many markets worldwide. Advanced machinery, digital controls, and a selection of materials merge in this complicated process, producing high-grade, durable items.
Understanding the Fundamentals of Plastic Extrusion
The process of plastic extrusion, often hailed as a foundation in the world of production, forms the bedrock of this discussion. Essentially, plastic extrusion is a high-volume production process in which raw plastic material is thawed and developed into a constant profile. It's a method commonly utilized for producing products with a continuous cross-sectional account, such as pipelines, home window frameworks, and weather condition stripping. The process starts with feeding plastic materials, usually in the kind of pellets, right into a heated barrel. There, it is warmed and blended up until it comes to be molten. The molten plastic is then forced via a die, shaping it into the wanted kind as it cools down and hardens.
The Duty of Various Products in Plastic Extrusion
While plastic extrusion is a generally used strategy in production, the products used in this process considerably influence its final output. Different kinds of plastics, such as abdominal, pvc, and polyethylene, each provide one-of-a-kind buildings throughout item. For circumstances, polyethylene, recognized for its resilience and versatility, is commonly made use of in product packaging, while PVC, renowned for its toughness and resistance to ecological factors, is utilized in building and construction. ABS, on the other hand, combines the most effective features of both, leading to high-impact resistance and toughness. The choice of product not just influences the item's physical residential or commercial properties but also affects the extrusion rate and temperature. For that reason, suppliers have to carefully consider the properties of the product to maximize the extrusion process.
Techniques Utilized in the Plastic Extrusion Process
The plastic extrusion process includes different methods that are critical to its procedure and efficiency (plastic extrusion). The conversation will begin with a simplified explanation of the essentials of plastic extrusion. This will certainly be followed by a breakdown of the process thoroughly and an expedition of approaches to enhance the performance of the extrusion strategy

Understanding Plastic Extrusion Essentials
In the world of manufacturing, plastic extrusion stands as a fundamental procedure, crucial in the manufacturing of a wide variety of daily items. At its core, plastic extrusion entails changing raw plastic material into a continual profiled form. This is achieved by thawing the plastic, commonly in the type of pellets or granules, and forcing it via a designed die. The resulting product is a lengthy plastic item, such as a pipeline, cable, or panel layer, that preserves the shape of the die. This cost-effective approach is extremely functional, able to produce complex forms and accommodate a wide range of plastic materials. Basic understanding of these fundamentals enables additional exploration of the extra elaborate aspects of plastic extrusion.
Thorough Extrusion Process Failure

Improving Extrusion Strategy Efficiency
Efficiency gains in the plastic extrusion process can substantially influence both the quality of the final product and the general efficiency of the operation. Continuous optimization of the extrusion strategy is vital to preserving a competitive edge. Regular maintenance of extrusion equipment can also decrease you can find out more downtimes, thus increasing performance.
Just How Innovation Is Altering the Face of Plastic Extrusion
The introduction of brand-new innovation has considerably changed the landscape of plastic extrusion. It has resulted in the advancement of advanced extrusion equipment, which has boosted the effectiveness and high quality of the plastic extrusion process. Advancements in the extrusion procedure have also been driven by technical developments, supplying improved capabilities and versatility.
Advanced Extrusion Machinery
Reinventing the realm of plastic extrusion, advanced equipment imbued with cutting-edge modern technology is ushering in a brand-new era of efficiency and accuracy. These machines, outfitted with ingenious attributes like automatic temperature level control systems, guarantee optimum problems for plastic processing, consequently decreasing waste and improving item high quality. While these improvements are already amazing, the constant evolution of modern technology guarantees even better jumps ahead in the field of plastic extrusion equipment.
Technologies in Extrusion Procedures
Taking advantage of the power of modern-day innovation, plastic extrusion processes are undertaking a transformative metamorphosis. With the advent of 3D printing, the plastic extrusion landscape is additionally expanding right into new worlds of possibility. These technical developments are not just enhancing the quality of extruded plastic items but additionally thrusting the sector towards an extra sustainable, reliable, and ingenious future.
Real-World Applications of Plastic Extrusion
Plastic extrusion, a versatile and effective procedure, locates use in plenty of real-world applications. The vehicle industry likewise utilizes this innovation to create parts like plastic and trim bed linen. The toughness and adaptability of plastic extrusion, coupled with its cost-effectiveness, make it a vital procedure across different sectors, underscoring its widespread practical applications.
The Future of Plastic Extrusion: Predictions and Patterns
As we want to the perspective, it comes to be clear that plastic extrusion is poised for significant innovations and transformation. New technologies promise to transform the market, from intelligent machinery that takes full advantage of effectiveness to lasting materials that minimize ecological impact. Automation and robotics are predicted to play a larger role, streamlining manufacturing and making sure consistent quality. Environmentally friendly choices to conventional plastic, such as bioplastics, are also expected to gain traction. These materials not just aid to save resources yet likewise lessen waste, straightening with worldwide sustainability goals. Advancements in 3D printing are forecasted to open up new possibilities for customization. These patterns show a dynamic, progressing future for plastic extrusion, driven by technological innovation and resource a dedication to sustainability.
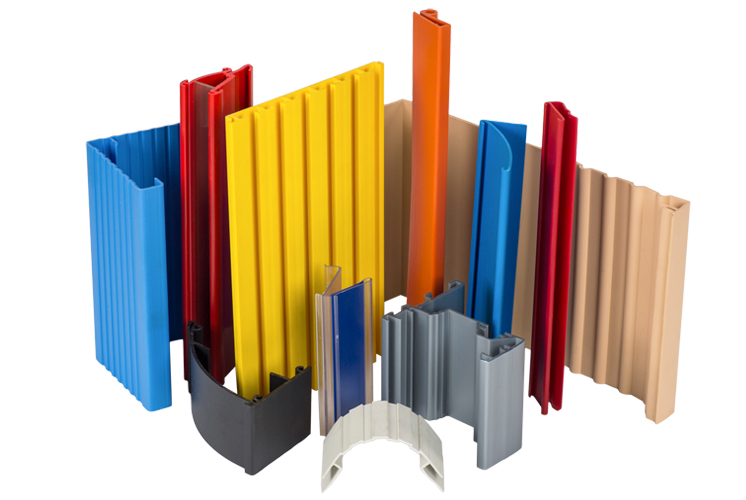
Final thought
To conclude, plastic extrusion is a complicated procedure that makes use of advanced technology and varied materials to produce varied items. Technical advancements, such click to read more as electronic controls, improve the manufacturing procedure and make certain consistent results. Moreover, the sector's concentrate on sustainability and smart machinery suggests an appealing future. As plastic production proceeds to progress, it continues to be a vital part of lots of industries worldwide.
In significance, plastic extrusion is a high-volume production procedure in which raw plastic product is thawed and formed into a continuous profile.While plastic extrusion is a frequently made use of strategy in production, the products utilized in this procedure considerably affect its final outcome. At its core, plastic extrusion entails changing raw plastic material right into a continuous profiled shape. It has led to the advancement of advanced extrusion machinery, which has actually boosted the performance and quality of the plastic extrusion process.In conclusion, plastic extrusion is a complex procedure that utilizes innovative modern technology and differed products to create varied products.
Report this page